High Pressure O-Ring Material Selection Guide
High pressure o-rings backup rings and seals require the right selection of material properties product configuration and groove design with the smallest clearance gap possible for optimal performance life. Marco Rubber offers a wide variety of high pressure o-ring materials for use with or without backup rings or consider metal spring energized PTFE seals for ultimate high pressure sealing performance.
Need help, contact an application engineer for assistance in selecting the best high pressure o-ring materials or product selection or groove design assistance from our expert team.
High Pressure O-Ring Material Compatibility
Compound # | Datasheet | Material | Hardness (Shore A) | Low Temp °F (°C) | High Temp °F (°C) | Features |
---|---|---|---|---|---|---|
B1001 | BUNA-N (NBR) | 90 | -40 (-40) | 225 (107) | Basic higher pressure applications | |
R1008 | HNBR | 90 | -10 (-23) | 350 (177) | Explosive decompression resistant tested to Norsok M-710 | |
E1121 | EPDM | 90 | -58 (-50) | 550 (288) | Explosive decompression resistant tested to Nace TM0297 excellent steam and good chemical resistance for use in georthermal environments | |
E1141 | EPDM | 95 | -58 (-50) | 550 (288) | Explosive decompression resistant excellent steam and good chemical resistance for use in georthermal environments | |
L1009 | Aflas® | 90 | 32 (0) | 482 (250) | Explosive decompression resistant tested to Nace TM0297 excellent with steam | |
L1010 | FKM Viton® | 90 | 5 (-15) | 482 (250) | Explosive decompression resistant tested to Nace TM0297 excellent with steam | |
V1007 | FKM Viton® | 90 | -15 (-26) | 437 (225) | Basic higher pressure applications | |
V1044 | FKM Viton® | 95 | -15 (-26) | 437 (225) | Ultra hard FKM for greater extrusion resistance | |
V1052 | FKM Viton® | 90 | -20 (-29) | 400 (204) | Explosive decompression resistant tested to Nace TM0297 excellent with acids fuels and wide range of chemicals | |
V1090 | FKM Viton® | 90 | -40 (-40) | 437 (225) | GLT Type FKM with wider temperature range for explosive decompression Norsok and Nace tested. | |
V1160 | FKM Viton® | 90 | -50 (-46) | 437 (225) | XLT Ultra Low Temperature Type FKM. Excellent high pressure and explosive decompression resistance. Norsok and Nace tested. | |
Z1322 | FFKM (Markez®) | 90 | -50 (-46) | 465 (241) | Lower temperature resistance AED explosive decompression resistance | |
Z1412 | FFKM (Markez®) | 90 | 5 (-15) | 590 (310) | Higher temperature AED resistance to Sour gas and associated chemicals and steam Compare to Kalrez® 7090 |
The information on this page is to the best of our knowledge accurate and reliable. However, Marco Rubber makes no warranty, expressed or implied, that parts manufactured from this material will perform satisfactorily in the customer's application. It's the customer's responsibility to evaluate parts prior to use.
The temperature ranges presented on this page are approximations for dry air service only and should not be used to determine design specifications or end-use temperature limits. Actual temperature range of a compound in an end-use application is highly dependent on part type, hardware configuration, applied forces, chemical media, pressure and thermal cycling effects, and other factors. The most practical way of determining an end-use temperature range is testing in the actual application conditions. Consult a Marco Engineer for more details.
High Pressure O-Ring Perfomance
Most o-rings are designed to operate at pressures up to 1,500 psi with an extrusion clearance gap of less than .04". At higher pressures and larger clearance gaps, the o-ring material must have enough strength to resist extruding into the clearance gap. The chart shows generally recommended pressure to clearance, gap of o-ring durometer with and without backup rings at typical room temperature.
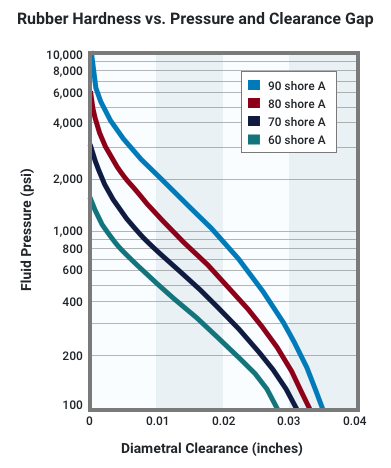
Chemical and High Temperature O-Ring Performance
Higher temperatures, chemical exposure and other application factors will impact need for even smaller clearence gap, increased durometer hardness or other improved material properties and groove design considerations to use backup rings or consider metal spring energized PTFE seals for use in high pressure applications.
Pressure Cycling O-Ring Performance
Cycling pressure can cause an o-ring to be repeatedly pushed against the clearance gap causing damage and sealing failures. Abrasion and extrusion resistant materials should be considered as well as smaller clearence gaps, backup rings or metal spring energized PTFE seals for pressure cycling applications.