O-Ring Permeation Chart
Learn About O-Ring Permeation Rate and Permeation Coefficients
Permeability or permeation of gases through an O-ring varies by material type; material hardness; degree of squeeze; presence or absence of lubrication; size of O-ring cross section; and the pressure, temperature and type of gas being sealed.
Typically, harder compounds containing more carbon black feature lower diffusion rates. Increased seal squeeze results in decreased permeability. Externally lubricated O-rings can decrease permeability.
FKM Viton® O-Rings are commonly used in vacuum applications due to lower permeation which impacts vacuum pump-down time and the ultimate vacuum level achievable. O-Ring permeation can also affect the accuracy of sensitive sensor and test equipment. O-Ring outgassing or leaching of internal substances can also impact sensor effectiveness. Marco Rubber offers FKM Viton® O-Rings with an additional post cure or vacuum baking resulting in lower outgassing O-Rings.
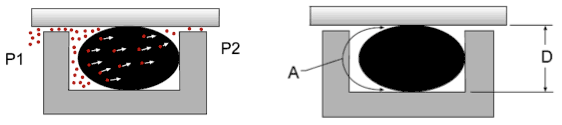
Q = K A (P1 - P2) / D
Permeation Coefficients (10-8 sccm - cm/sec - cm2 - atm)
Material | HE | H2 | H20 | N2 | CO2 |
---|---|---|---|---|---|
Buna-N | 8 | 2.5 | 760 | 0.1 | 25 |
EPDM | 25-30 | 16-18 | 6-7 | 85 | |
Silicone | 250 | 75-450 | 8000 | 200 | 2000 |
Fluorosilicone | 140 | 80 | 40 | 400 | |
FKM Viton ® A | 9-22 | 1-2 | 40 | 0.05-0.7 | 5 |
FKM Viton ® GF | 30 | 3 | 2 | ||
Markez ® FFKM | 60-80 | 6-8 | 90-100 | 8-12 | |
KEL-F | 0.1 | 0.1 | 0.5 | ||
PTFE | 0.4 | 0.14 | 0.12 | ||
Polyimide | 1.9 | 0.1 | 0.3 | 0.2 |